Cement tank trucks are specialized for transporting bulk goods such as fly ash, cement, lime powder, mineral powder, and granular alkali, while regular trucks can transport a wide variety of goods including steel products, daily industrial goods, minerals, and construction materials. The primary difference lies in the structure of their cargo compartments. Cement tank trucks have cylindrical tanks designed specifically for transporting cement, whereas regular trucks have open cargo compartments suitable for various goods. Understanding these differences is crucial for selecting the right vehicle for your transportation needs. This article provides a detailed comparison of cement tank trucks and regular trucks.

Table of Contents
Design and Function of Cement Tank Trucks and Regular Trucks
Cement Tank Trucks
The basic structure of a cement tank truck includes a truck chassis, extractor, air compressor, air pipeline, tank, and loading/unloading devices. The tank is the core component, designed for loading and transporting cement or other bulk materials. Inside the tank, components like tank heads, cylinders, manhole covers, and liquefaction devices ensure efficient loading and unloading. Cement tank trucks use pneumatic systems for loading and unloading cement, making them essential for construction sites and roadworks.
Compared to regular trucks, cement tank trucks feature cylindrical tanks that use gravity and liquefaction devices to prevent cement from clumping during transportation, facilitating easy unloading. These trucks are equipped with pneumatic systems to ensure fast and efficient operations.
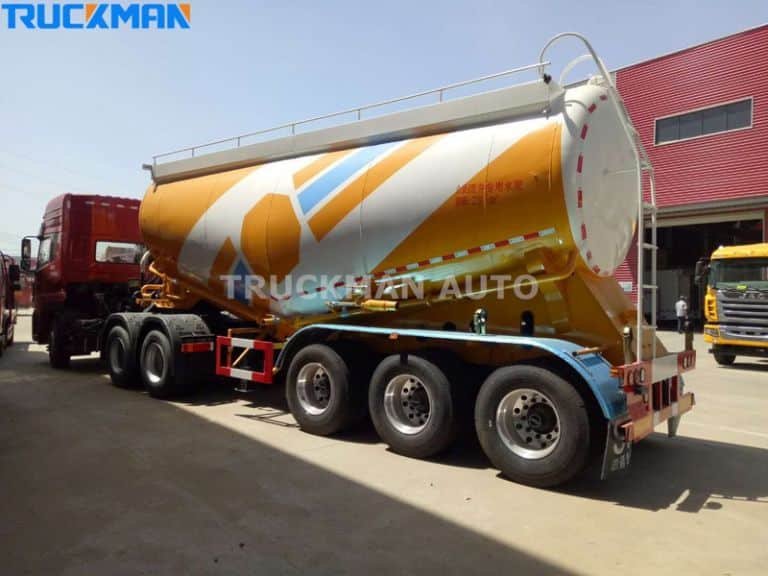
Regular Trucks
Regular trucks have rectangular cargo compartments, some equipped with automatic tipping mechanisms, suitable for transporting specific goods like furniture, clothing, and non-perishable foods. The choice of unloading method depends on the characteristics, quantity, and weight of the goods, as well as the conditions and equipment available at the unloading site. Regular trucks are widely used in daily goods transportation and logistics, efficiently handling various types of cargo.
In contrast to cement tank trucks, regular trucks’ cargo compartments are usually rectangular or square, providing flexibility to transport a variety of goods. Their operation is relatively simple and can be adjusted according to different cargo types and transportation needs, making them ideal for industries like furniture transport, clothing distribution, and food supply.
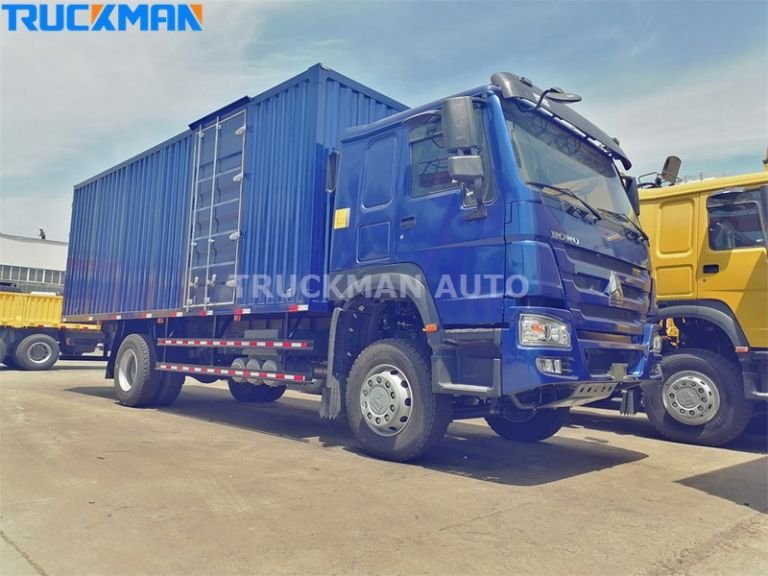
Key Differences
Cargo Compartment Structure Differences
Cement Tank Trucks: The tank of a cement tank truck consists of the tank itself and a support structure. The tank, typically made of steel plates with special welding techniques, ensures durability and resistance to cracking. The support structure, made of steel pipes, supports the tank’s weight, preventing it from shaking during transit. A buffer device between the tank and the truck body reduces collisions and vibrations, preventing cement clumping inside the tank.
Regular Trucks: Regular truck cargo compartments vary widely to meet different transportation needs. For example, box-type compartments are fully enclosed, suitable for transporting small goods or serving as refrigerated trucks for transporting fruits, vegetables, seafood, and pharmaceuticals.
Operation and Maintenance Differences
Cement Tank Trucks: Operating a cement tank truck involves multiple aspects, including operational skills, maintenance, and safety procedures, requiring specialized knowledge and skills. Regular maintenance is key to ensuring good operational status, including periodic replacement of worn parts, cleaning cement residues and dust inside and outside the tank, and maintaining a clean tank appearance.
Regular Trucks: Operating regular trucks is relatively simpler but still requires adherence to traffic regulations and extensive driving experience. Maintenance involves daily operational procedures, regular inspections, using qualified spare parts, and keeping maintenance and repair history records. Key inspections include the cargo compartment and tire conditions.

Factors to Consider When Choosing the Right Vehicle
Several factors need to be considered to ensure the chosen vehicle meets personal needs, budget, and long-term satisfaction. Key factors and related examples include:
Need: Determine the type of goods to be transported. Choose a cement tank truck for bulk cement and a regular truck for bagged cement or other general goods. For example, a construction company frequently transporting large amounts of bulk cement might choose several cement tank trucks to improve transportation efficiency.
Budget: Set a reasonable budget to narrow down vehicle options and avoid overspending or buying overly simplistic models. A small logistics company with a limited budget might choose a cost-effective regular truck to meet daily transportation needs without overspending.
Power Performance: Consider engine type, displacement, maximum power, and torque, affecting acceleration and top speed. For instance, a transport company needing to haul heavy goods in mountainous areas might choose a regular truck with strong torque and good climbing ability.
Fuel Economy: The fuel consumption level directly impacts long-term use costs, making low-fuel consumption models preferable to reduce operating costs. A cross-city transport company aiming to lower long-term fuel costs might choose several fuel-efficient regular trucks.
Safety: Check vehicle safety features and ratings, such as braking systems and body structures, to ensure driving safety. A large logistics company focusing on safety might choose regular trucks equipped with advanced safety features like anti-lock braking systems and stability control systems.
Configuration and Technology: Consider high-tech configurations like navigation systems, rearview cameras, and driving assistance features to enhance driving convenience. A delivery company aiming to improve efficiency and driver experience might choose regular trucks with advanced navigation systems and rearview cameras.
Maintenance: Understand the brand’s after-sales service network and maintenance costs to ensure timely service and support in the long term. Regular maintenance is key to ensuring good operational status, including periodic replacement of worn parts and cleaning residues and dust.
Conclusion
The main difference between cement tank trucks and regular trucks lies in the cargo compartment structure. Cement tank trucks have cylindrical tanks specifically for transporting bulk cement, while regular trucks have open or closed compartments suitable for bagged cement and other goods. Choosing the right transportation tool depends on the type of goods to be transported. Cement tank trucks offer unique advantages in transportation efficiency and specialization, while regular trucks hold a significant position in logistics and distribution due to their versatility.
Selecting the right vehicle affects current transportation efficiency and future maintenance and resale value. Cement tank trucks are suitable for companies frequently transporting bulk building materials, while regular trucks are ideal for logistics and distribution companies transporting various goods. In the long run, choosing the right vehicle can significantly reduce operating costs, improve transportation efficiency, and ensure high operational efficiency in respective fields.
FAQ
The main function of a cement mixer truck is to transport concrete from the factory to the construction site while keeping the concrete uniformly mixed by rotating the mixing drum, preventing separation and solidification.
A cement mixer truck mixes concrete by rotating the mixing drum. The spiral blades inside the drum turn the concrete over, ensuring uniformity and preventing solidification.
Cement mixer trucks are generally more expensive than regular trucks due to their specialized mixing equipment and more robust chassis. Their maintenance and operating costs are also higher.
Regular trucks can transport various goods such as steel products, industrial goods, building materials, furniture, clothing, and food. Their cargo compartments are designed to adapt to different transportation needs.
Cement mixer trucks require maintenance every 5,000 to 10,000 kilometers, including checking and replacing lubricating oil, hydraulic oil, etc. The inside of the mixing drum also needs regular cleaning.