A cement tanker trailer is suitable for transporting and unloading granular materials such as fly ash, cement, lime powder, and ore powder by pneumatic pressure. The volume of these trailers is generally between 35-45 square meters.
Cement tanker trailers use the power of a self-powered engine to drive the onboard air compressor through the extractor. This setup sends compressed air through the pipeline into the air chamber in the lower part of the sealed tank.
The cement on the fluidized bed is suspended in a fluid state and transported when the pressure in the tank reaches the rated level. When the pressure in the tank reaches the rated value, the discharge butterfly valve opens, and the fluidized cement is conveyed through the pipeline.
The role of the air compressor is vital. This article will focus on the relevant knowledge of the air compressor.

Table of Contents
What Is a Cement Tanker Trailer Air Compressor?
A cement tanker trailer air compressor is a mechanical device that compresses gas to a certain pressure. It usually consists of several key components: a motor, compressor, exhaust system, cooling system, and control system. Each part plays a crucial role in the efficient operation of the compressor.
Air compressors can be divided into many types depending on the characteristics of gas pressure, exhaust method, and gas type. These include piston air compressors, screw air compressors, centrifugal air compressors, and rotary air compressors, each suited for specific industrial applications.
Working Principle of Air Compressor
The working principle of the air compressor is to compress oxygen-containing gas (e.g., air) using machinery such as a piston or screw. This process increases the gas pressure, allowing it to be supplied to the required equipment. The specific working principles are as follows:
Compression Process: Air enters the air filter and, after filtering, it moves into the compressor. Through a specific compression process (such as piston movement or screw rotation), the air is compressed to a certain pressure. This step is crucial for ensuring the air is clean and suitable for use.
Discharge Process: The compressor discharges the high-pressure gas through the discharge pipe. It also inhales air again through the inlet valve. This cycle keeps a steady supply of compressed air. It ensures that the connected equipment can work nonstop.
Cooling Process: During compression, the gas generates a lot of heat. To ensure the normal operation of the compressor, this heat needs to be dissipated through a cooling system. Proper cooling prevents overheating and maintains the efficiency and longevity of the compressor.
Understanding these processes shows the complexity. It also shows the importance of keeping an air compressor in good condition.
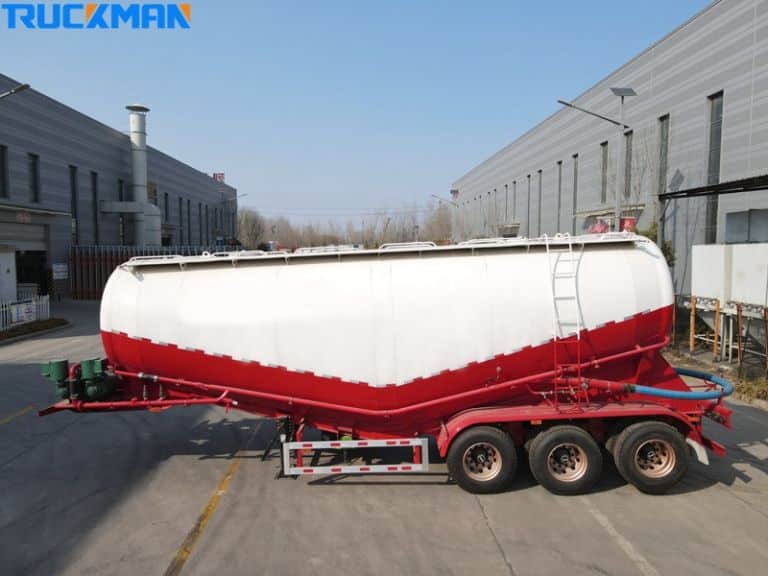
Main Function of Air Compressor
A cement tanker trailer air compressor is a machine that compresses air into high-pressure gas. This process is essential for various operations in a cement tanker trailer. The air compressor’s main function is to make sure that it efficiently moves and unloads granular materials, like cement and fly ash.
Inside the air compressor is a circulatory system. It consists of a crankshaft, connecting rod, and piston. They work to compress the air. Here’s how it works:
Air Intake: The air is sucked into the compression chamber through the intake valve.
Compression: With the downward movement of the piston, the air is compressed, increasing its pressure.
Storage: The compressed gas is then sent to the air storage tank, where it is held under high pressure.
Release: When needed, the high-pressure air is released from the storage tank. It powers various functions, such as unloading cement from the trailer.
This process is systematic. It ensures that the air compressor provides a reliable supply of high-pressure air. This air is crucial for the cement tanker trailer to work well.
Common Uses of Air Compressor
Air compressors for cement tanker trailers are widely used in many industries. They are versatile and efficient. Here are some common applications:
Mining: In mining operations, air compressors provide the power. They power pneumatic tools and equipment. They are essential for drilling, blasting, and material handling. They ensure smooth and efficient mining.
Machinery: Air compressors are integral to the operation of various machinery. They power pneumatic systems. These systems drive automation in manufacturing plants. They boost productivity and cut manual labor.
Chemical Industry: In the chemical industry, air compressors are used to transport gases and liquids through pipelines. They are also crucial in processes such as refrigeration, aeration, and the production of compressed gases.
Metallurgy: Air compressors play a vital role in the metallurgy industry by powering tools used in the smelting and refining processes. They ensure steady pressure for air-powered hammers, drills, and other equipment. The tools are used in metalworking.
Fly Ash Tanker: In fly ash tankers, the air compressor provides air. It powers the suction to remove settled fly ash and keep the tank clean. This process ensures efficient unloading. It also prevents blockages. It keeps the tanker clean and working.

Advantages of Cement Tanker Trailer Air Compressor
High Efficiency and Energy Saving: The air compressor is known for its high efficiency and energy-saving characteristics. It operates stably and reliably, meeting the diverse needs of users. For instance, modern air compressors can cut energy use by up to 30%. This makes them a cost-effective choice for the industry.
Low Noise and Environmentally Friendly: The noise level of the air compressor is remarkably low, making it more environmentally friendly. This feature ensures that the surroundings are not disturbed. This is key in residential or noise-sensitive areas. Low-noise operation contributes to a healthier work environment for operators.
High Degree of Automation and Safety: The air compressor has advanced automation. It makes it safer and more efficient. It can detect and address faults in real time, reducing downtime and preventing potential hazards. For example, automated diagnostics can alert operators to maintenance needs before issues escalate.
Ease of Maintenance: Regular maintenance is crucial to ensure the normal operation of the air compressor. You must regularly check machine settings. You must do routine tasks like oil changes, filter replacements, and system inspections. Proper maintenance extends the lifespan of the air compressor and ensures optimal performance.
Precautions For Buying Cement Tanker Trailer Air Compressor
Selection principles: The selection of air compressors for bulk cement trucks needs to take into account the type of gas, gas pressure, gas supply, and other factors. At the same time, we need to consider the performance of different machine models on the market. We must consider price, maintenance costs, and other factors. These factors are key to a comprehensive assessment of the selection program.
Maintenance: You need to do regular maintenance on the air compressor. Pay extra attention to cleaning and maintaining the filter and cooling system. If you find faults need to be repaired promptly to avoid adverse effects on the normal work of the bulk cement truck.

Summary
Truckman Automobile understands that a cement tanker trailer air compressor is a crucial accessory. It directly affects the efficient loading and unloading of goods. It is indispensable. It transforms granular materials like cement, fly ash, and lime powder into a fluid state for transport. Therefore, choosing the right air compressor is of paramount importance.
Choosing the right air compressor involves considering many factors. These include the type of gas, needed gas pressure, and your specific needs. By thoroughly evaluating different models, you can see their performance, price, and maintenance costs. This lets you make an informed decision that ensures reliability and efficiency.
We are here to help. Our team at Truckman Automobile is dedicated to providing you with detailed purchase plans and expert advice. We can guide you through picking. You will choose an air compressor that perfectly meets your needs.
FAQ
An air compressor’s life is related to many factors. It can last 10-15 years. However, proper care and maintenance can extend its life.
Proper care and maintenance are very important to extend the service life of the air compressor.
Regularly replace and clean the internal parts of the air compressor, such as the air filter, oil filter, oil-air separator, etc.
Regularly remove dust and dirt from the outside of the air compressor and check for damage or cracks.
Check the working condition of gauges such as pressure gauges, safety valves, and controllers to ensure their accuracy.
Ensure that the air compressor is operated under temperature and humidity conditions within the normal range.
Reduce the load on the air compressor as much as possible and avoid overloading the air compressor for a long time.
Ensure that every joint and connection of the air compressor is secure to avoid air leakage etc.
Excessive noise: If the noise of the air compressor is too loud, it may be caused by the wear of machine parts or loose bearings. The treatment methods are as follows: carry out maintenance on the air compressor and replace the parts regularly; make sure whether the bearings are loose, if they are loose, they need to be reinstalled or replaced.
Air Leakage: Air leakage from the compressor is a very common problem, usually due to poor sealing or clogged piping. Treatment methods are as follows: check whether the seals play a sealing role, and clean up the pipeline, as far as possible to reduce gas leakage.
Strange noise: If the compressor has strange noise, it may be caused by the structure of the equipment itself, or it may be caused by the wear and tear of the parts or loosening. Handling methods are as follows: confirm which parts have abnormal noise and repair or replace them in time; replace the parts with new ones to improve the quality of the air compressor.
Overheating: If the compressor is overheating, it may be caused by the wear of internal parts or insufficient lubrication oil. Handling methods are as follows: confirm whether the lubricating oil is sufficient; if it is caused by wear and tear of the parts, repair or replace the parts in time.