Fuel tanker trailer is a mobile container, the container are filled with a variety of flammable and explosive oil materials, so it also becomes a mobile source of danger at any time. Quality control and inspection can reduce the danger and play a vital role in improving the tanker trailer.
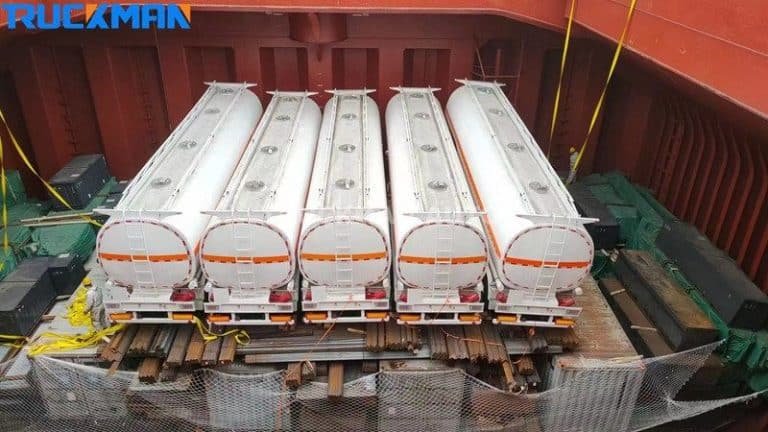
Table of Contents
Quality Control in Fuel Tanker Trailer Manufacturing
Significance of quality control: Quality control can not only reduce the impact of fuel tanker trailer quality problems, but also improve the quality, reliability and consistency of products. It can also improve customer satisfaction and maintain a good reputation, thus gaining an advantage in the fierce market competition. The most important thing is to ensure the safety of the fuel tanker trailer.
Quality control process: Collect the laws and regulations about fuel tanker trailers, prepare the quality plan for the design process control, draw the product drawings, prepare the process and finished product test procedures, monitor the production process, and the related side leakage prevention test for the finished vehicle.
Fuel Tanker Trailer Critical Mass Inspection
Water filling test: Hydro-testing is mainly done by injecting water into the tank and observing the pressure. Before pressurizing the tank for hydro-testing, it is necessary to confirm that the connections of the piping joints, valves, covers, etc. are well sealed before testing. Before the pressure inside the tank drops to 0, the connections must not be disassembled to ensure safety.
Air pressure test: The detection is mainly carried out by means of pressurization. The inspector needs to connect the pressure gauge to the tank, and then hold the pressure for a certain period of time after the pressure is raised to a certain value, observe the changes in the pressure gauge, and judge whether there are problems such as leakage.
Material test: Fuel tanker trailer tanker body is generally made of corrosion-resistant alloy steel to ensure the sealing and protection of diesel fuel. Inspection of the tanker body material needs to pay attention to its strength, corrosion resistance, withstand pressure and load requirements.

Improved Safety Through Leak Detection And Prevention Testing
In addition to the testing methods described above, there are other specific tests for preventing leaks and malfunctions. For example, the use of more advanced acoustic waves, radiography, etc. improves the accuracy of testing.
Ultrasonic detection: mainly through the reflection and propagation of ultrasonic waves to carry out detection. The inspector needs to place the ultrasonic probe on the surface of the tank, and then receive the reflected ultrasonic signals through the instrument, analyse the changes in the signals, and judge whether there are defects or damage to the tank.
Ray detection: mainly through the scattering and absorption of rays when they pass through the material to carry out detection. The inspector needs to place the ray source on one side of the tank, and then place the ray detector on the other side to collect the ray signals passing through the tank, and analyse the changes of the signals to judge whether there are defects or damages in the tank.
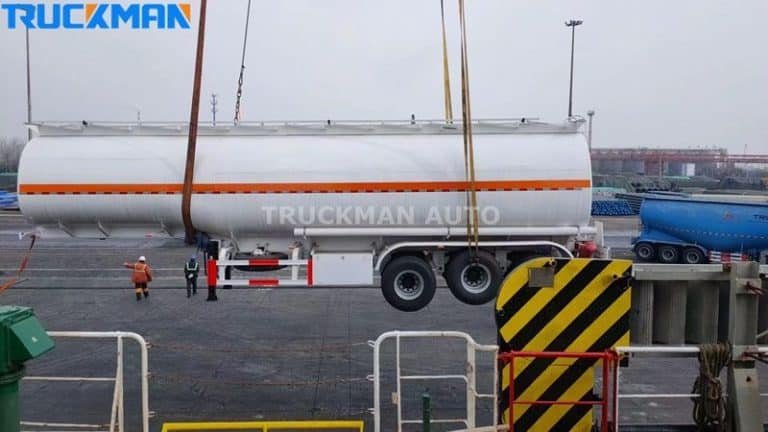
Summary
Strict quality control and testing of tanker trucks is to ensure the safety of vehicle operation and the accuracy of oil metering. Because tanker trailers are susceptible to external forces and natural factors over long periods of time, if they are not tested and repaired in a timely manner, they may cause vehicle breakdowns, oil leaks, and other safety issues.Fuel tanker trailer manufacturers need to continually improve the quality control of their vehicles as well as their testing in order to achieve the maximum degree of safety.